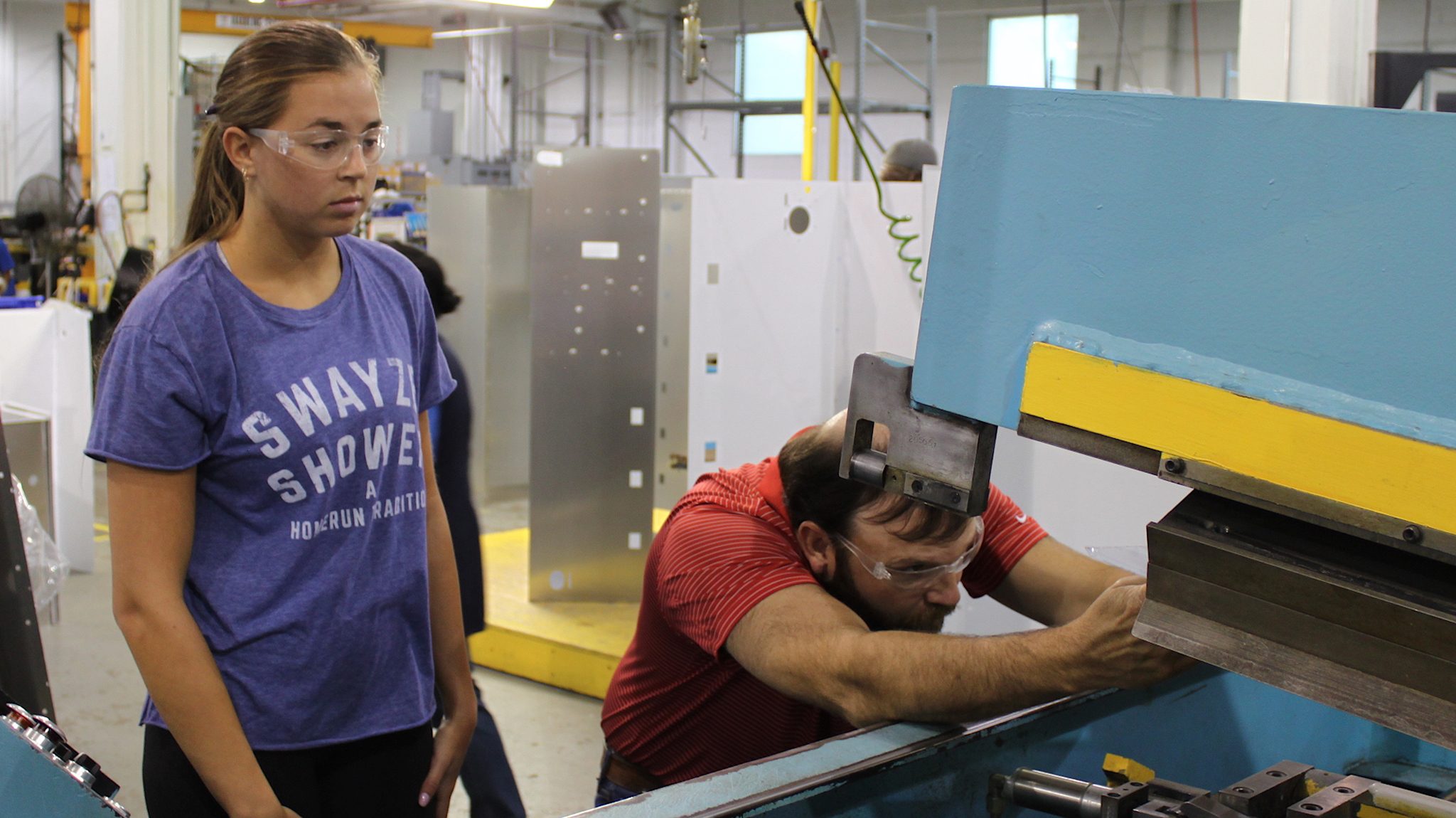
Center for Manufacturing Excellence student Miller Myers (left) watches as Sam Pigott, Viking Range plant manager, adjusts equipment at the manufacturing plant in Greenwood. Photo by Shea Stewart/University of Mississippi
GREENWOOD, Miss. – The Viking Range plant rumbles on this late summer afternoon with an orchestra of thundering industrial sounds.
The clank of punching metal tolls across the airplane hangar-sized space. Forklifts beep as they cruise across the plant’s concrete floor. Voices boom out. Enveloping the dull manufacturing roar is the drone of the massive plant’s air conditioning grappling with the oppressive heat of a Mississippi summer.
Slicing through all these noises arrives an oddity: the calypso beat of the royally named Amada Vipros 357 Queen, a 15-ton punch press machine whose labor rings across the factory floor with a tinkling like a steel drum as it fabricates metal, a first step in creating world-renowned, professional-grade kitchen ranges for home use.
The University of Mississippi students gathered around the machine aren’t distracted by its Caribbean rhythm, though. These Center for Manufacturing Excellence, or CME, students are focused on how to make this machine more efficient and effective and improve Viking Range’s manufacturing process.
It’s all part of their MANF 450 class, a CME course that offers knowledge about traditional problem-solving methods used by industries.
“The CME mission is to prepare great students who make great things, and these classes highlight the versatility and preparedness of our students while providing them the opportunity to learn about manufacturing in Mississippi,” said Matt O’Keefe, CME executive director and UM professor of chemical engineering.
“Through these classes, and being exposed to real manufacturing and work environments, it allows students to gain a unique perspective and apply the practical skills needed to work in the manufacturing sector.”
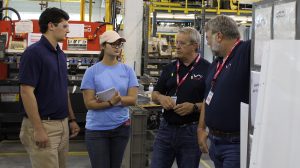
Center for Manufacturing Excellence students Branden Livingston (left) and Catherine Teh discuss the manufacturing process at Viking Range in Greenwood with CME extension service instructor Eddie Carr and Jack McClurg, associate professor of practice at the center. Photo by Shea Stewart/University of Mississippi
A week before the fall semester officially began, the 44 Ole Miss students in the class fanned out across Mississippi manufacturing sites, with 15 students visiting Ingalls Shipbuilding in Pascagoula, 14 students going to Viking Range in Greenwood and 15 students spending time at VIP Cinema Seating in New Albany.
At each plant, students were divided into three groups and tasked with solving a specific problem on the respective factory floors. For some students at Ingalls, that meant addressing damage prevention when installing sensitive communications cabling on U.S. Navy guided missile destroyers.
At VIP Cinema Seating, one challenge was solving how cup holders were becoming loose and easily removed from the seats. And at Viking Range, a quartet of students looked at increasing the effectiveness of the calypso-creating Amada Vipros 357 Queen.
After their visits, students created presentations for both company executives and CME professors and staff about their specific problem and how they would solve it.
Manufacturing is important to the Mississippi economy, with almost 146,000 Mississippians employed in manufacturing in August, according to the U.S. Bureau of Labor Statistics. And the class demonstrates how the university is preparing Mississippi’s next generation of manufacturing leaders while assisting a vital sector of Mississippi’s economy right now.
“It also allows Mississippi manufacturers to highlight their companies and recruit talented, young accountancy, business and engineering professionals right here in Mississippi,” O’Keefe said. “We feel that relationship is truly beneficial and supports statewide objectives that have identified workforce development for advanced manufacturing as a high priority.”
The MANF 450 class is led by Eddie Carr, an extension service instructor at the CME. Besides teaching classes, Carr is often out of the classroom and away from campus, traveling the state and developing relationships with Mississippi-based companies.
“Our outreach programs are vital to the CME assisting Mississippi manufacturers and understanding and practicing the skill set needed for CME students coming out of college,” O’Keefe said. “Instructors like Eddie Carr travel throughout the state to work with companies and identify ways in which our program can be an asset.
“This may be assisting with curriculum, participating in experiential learning classes, developing student projects or potentially providing them with highly talented and versatile young professionals as interns, co-ops or permanent employees.”
One recent success arising from Carr’s ambassador work and involving innovative CME students being an asset to a Mississippi company was students assisting the nonprofit The Baddour Center in Senatobia with a manufacturing challenge that involved how best to package coffee condiment kits for inclusion on FedEx planes.
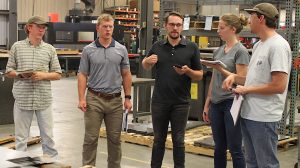
Students in the Center for Manufacturing Excellence visit Viking Range in Greenwood to learn more about traditional problem-solving methods used by industries. Students (from left) Jacob Commer, Ridge Brohaugh, Jonathan Gibson, Hope Walker and Tyler D. Butler discuss how to improve a Viking process. Photo by Shea Stewart/University of Mississippi
Carr describes the experiential learning classes such as MANF 450 as a win-win for the students and for the industries that host the student groups.
“The industries can utilize teams of highly talented students to provide a fresh look at solving quality and throughput problems while removing waste and cost from their production processes,” said Carr, who joined UM in April 2018 after a career in manufacturing.
“Additionally, the industries can utilize student visits as a recruiting tool for employing interns, co-op students and new graduates. The students are able to practice their classroom lecture topics on real-life challenges on the industry’s factor floor.”
For Tyler A. Butler, a senior mechanical engineering major from Picayune, his real-life challenge found him donning safety glasses and closely watching the Amada Vipros 357 Queen at Viking and devising a method with his student group to reduce the amount of scrap metal it created.
Students decreased scrap rates in the punch press process by measuring hit numbers and predicting the degradation of these tools.
“We were able to determine a maximum usage number for the tool before it will go bad,” Butler said. “With this predictability, Viking’s process will be more efficient and scrap will be reduced due to dull tools, thus saving the company money.”
Other groups tackled their challenges with similarly novel approaches, such as the issue of VIP Cinema Seating having problems with cup holders coming loose in their luxury movie theater chairs.
“We recommended a companywide standardized process on how to insert the cup holders,” said Stuart Gunner, a senior managerial finance major from Olive Branch. “We also came up with a cutting guide for one of their models to ensure that all cuts they made would be the same.”
Beyond solving problems for Mississippi manufacturers, the class also gave students confidence in their burgeoning skills and knowledge, and taught them the value of teamwork when working with fellow students from diverse majors such as accountancy, business and engineering.
“Being able to work in a team is a very important skill that engineers use,” said Chet Wilson, a senior mechanical engineering major from Pontotoc, whose team visited Ingalls. “I was able to gain experience in teamwork, communication and problem-solving during this class.
“This will help me in my future career, as I hope to find a job that will allow me to work in a team and use my skills as an engineer.”
None of the problems the students encountered were easy. As Carr reminded a group of students at Viking, “If (these problems) were easy to fix, they’d be fixed already.”
But the solutions the students generated were well-received, both by company executives and by CME professors and staff.
Providing these senior-level students with an introduction to problem-solving techniques used in many industries and consulting firms is one of the objectives of the class, Carr said. But he also wanted the students to use their creativity and determination.
The students met that challenge head-on, and in the process, Mississippi manufacturing became more efficient and effective, and the students received an experience of a lifetime.
“The most enjoyable aspect of the visit, for me, was the knowledge and real-world experience that I obtained from the trip,” Butler said. “Moreover, I valued the experience because it allowed me to conduct the problem-solving techniques I had learned in my CME classes.
“I believe problem-solving techniques and experiences are extremely important to my success in whatever career I wind up choosing.”