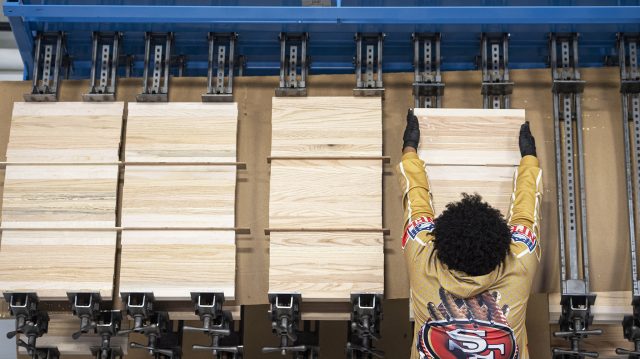
Kaysha Watson, a sophomore mechanical engineering major from Jackson, glues board together during the first process of a manufacturing lab in the UM Haley Barbour Center for Manufacturing Excellence. The exercise was part of an experimental class offered during the university’s Winter Intersession. Photo by Logan Kirkland/Ole Miss Digital Imaging Services
OXFORD, Miss. – Several University of Mississippi students received intense, hands-on manufacturing instruction when two trainers from the Toyota Motor Manufacturing Mississippi plant in Blue Springs spent time with them on campus during Winter Intersession.
Toyota Production System group leaders Jesse Corley and Tiffany Prude assisted in teaching Manf 255: Takt Time and Standard Work, one of three experimental classes offered in the UM Haley Barbour Center for Manufacturing Excellence.
The word “takt” is a reference to the pace or rate at which customers demand a product to be made. “Standard work” is the term used globally by companies to define a process by listing the exact steps and sequence required to complete the process correctly.
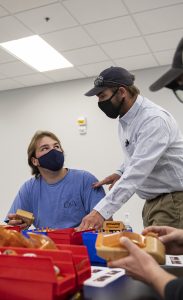
Jesse Corley (right), of Toyota Training, teaches sophomore mechanical engineering major Carter Brown, of Ocean Springs, about the Toyota Production System. Photo by Logan Kirkland/Ole Miss Digital Imaging Services
During their two-day classroom session, the sophomore students learned these practices and developed a manufacturing line using toy cars. During this exercise, they had to focus on efficiency, takt time and defect rates.
“Students spent a great deal of time learning about the ‘seven deadly wastes’ in a manufacturing organization, and how to remove waste from a process,” said Eddie Carr, professor of practice and the course’s instructor.
“The Toyota TPS trainers also exposed the students to ‘kaizen,’ which is a term for ‘continuous improvement.’ Students learned to examine a process used to manufacture a product and utilize the kaizen process to improve the step or steps that limit improved production output.”
After two days of learning part of the Toyota Production System, the students were organized into seven-to-eight-person teams. Each team met in the CME lab for a three-hour experiential learning exercise of making wooden cutting boards through a seven-step process.
Initially, each team member volunteered to operate one of the seven pieces of woodworking equipment, and the process was started with each member passing a product to the next stage once their operation was complete.
“The students’ training helped them immediately recognize that the seven processes had widely varying times to complete the process,” Carr said. “This led to some operators working at a frantic pace, and some operators waiting long periods of time for the next cutting board to be presented to their operation.”
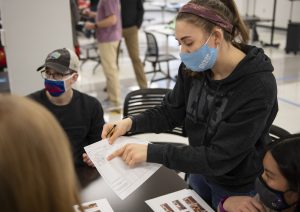
UM sophomores Maren McSparin (standing), a chemical engineering major from Edwardsville, Illinois; Andrew Duffield (left), of Murfreesboro, Tennessee; and Francesna Patawaran, of Tupelo, review the takt time for a toy car assembly process in the Haley Barbour Center for Manufacturing Excellence during a Winter Intersession class led by Toyota Production System group leaders. Photo by Logan Kirkland/Ole Miss Digital Imaging Services
After running an initial trial of six cutting boards, teams were asked to regroup and take half an hour to sketch out an improved equipment layout to minimize motion and transportation – two of the “seven deadly wastes” – and recommend a staffing plan to minimize the imbalance in work content across the seven processes.
“Each team returned to the lab area with a plan that combined some operations such that one operator ran more than one machine, which subsequently led to moving equipment to reduce the wasted motion and transportation by the operators,” Carr said. “Of the four teams that rotated through the lab exercise over a two-day period, three teams staffed the line with four operators and one team ran the cutting board line with only three operators.
“Each team made tremendous progress in eliminating the wasted time due to the imbalance in the process, while making the work area safer and easier to operate.”
Students said the time spent with the Toyota reps was informative and inspirational.
“The two trainers did an excellent job of sharing Toyota’s training on standardized work, line balancing and continuous improvement,” said Maren McSparin, a sophomore chemical engineering major from Edwardsville, Illinois. “Through their presentation, we had some interactive activities, which gave us a foundation in determining takt time and cycle time.”
The training emphasized the human aspect of work and provided a new perspective on how balancing a line gives each operator an amount of work that truly contributes to the success of a project and, ultimately, the company, said Carter Brown, a sophomore mechanical engineering major from Ocean Springs.
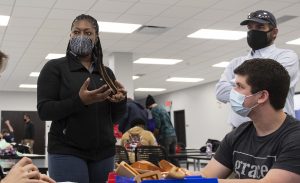
Tyler Blaylock (right) a sophomore mechanical engineering major from Madison, learns about takt time and standardized work from Toyota Training reps Tiffany Prude (standing, left) and Jesse Corley (upper right). Photo by Logan Kirkland/Ole Miss Digital Imaging Services
“Overall, the Toyota Production System training came to life as we exercised the ‘Toyota way’ in the manufacturing of our beautiful cutting board,” McSparin said. “Overall, this class has made me more prepared for future internships and a future career.”
Prude said she was impressed that students learned so much at such a rapid pace.
“They learned teamwork and how to come together as a group to make decisions,” she said. “Brainstorming skills were developed in the sense of having to deal with change points within the process and when sudden changes were introduced to make adjustments.
“They also learned the power of benchmarking from others and bringing those original ideas back to their groups. They learned how to create visuals on the standard TPS documents.”
CME administrators are grateful for their relationship with the auto manufacturing company, said Tyler Biggs, the center’s admissions and marketing specialist.
“Toyota is one of the many Mississippi companies that host our students over the year,” he said. “This relationship has grown over the last couple of years as we have seen an increase in CME students hired by Toyota.”