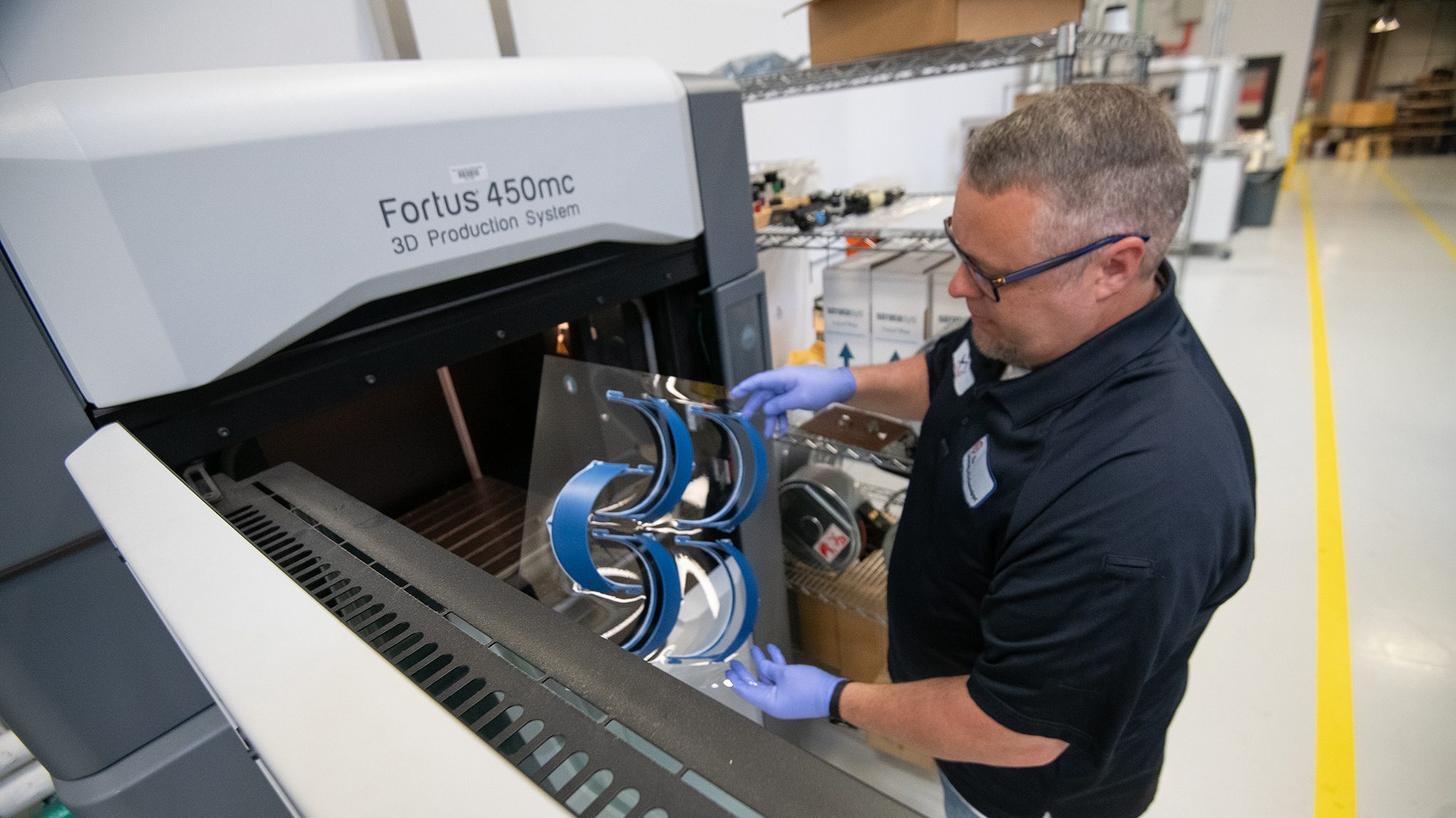
Andy Gossett, a technical support staff member at the UM Haley Barbour Center for Manufacturing Excellence, removes a batch of 3D-printed headbands from one of the facility’s printers. The headbands will be used for face shields by health care workers at Baptist Memorial Hospital-North Mississippi in Oxford during the COVID-19 pandemic. Photo by Kevin Bain/Ole Miss Digital Imaging Services
OXFORD, Miss. – In an effort to support local health care workers responding to the COVID-19 pandemic, two University of Mississippi units are using 3D printers to produce personal protective gear that is in short supply.
The Haley Barbour Center for Manufacturing Excellence and the IDEAlab in the J.D. Williams Library are printing face shields that will be donated to Baptist Memorial Hospital-North Mississippi in Oxford.
CME staff is working directly with Dr. Will King, a radiologist at Radiology Associates of Oxford who contracts with the hospital, said Scott Kilpatrick, the center’s associate director of academic programs. King, who has a 3D printer at home, has experimented with various designs for physical protection equipment, or PPE, that can be printed and used by health care workers during the outbreak.
“Here on campus, we are fortunate to have resources in places like the CME and the IDEAlab that can provide support in some way,” Kilpatrick said. “Even individual UM faculty and staff are using their own personal 3D printers to contribute as best they can.”
The face shields are important because they help conserve the much-needed N95 masks that are in short supply. The headbands are reusable with an interchangeable face shield, which greatly increases their utility versus a single-use disposable design.
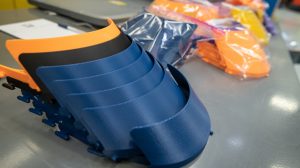
A batch of headbands 3D-printed at the Haley Barbour Center for Manufacturing Excellence waits to be packed and delivered to Baptist Memorial Hospital-North Mississippi in Oxford. Photo by Kevin Bain/Ole Miss Digital Imaging Services
After consultation with other medical staff at the hospital, King settled on a design that was publicly posted on the National Institutes of Health website. This design provides an open-source model for headbands that can be used to support clear plastic face shields for medical staff.
King’s group purchases inexpensive clear presentation covers and punches them with a three-hole punch. Using this method, the clear cover can be thrown away after use, and the headband can be used multiple times.
“Our goal is to produce around 400 prints by the end of the month at the latest,” Kilpatrick said. “After assessing our print process and capacity, it was determined that the CME would need to print around the clock in order to make sure that demand will be met.”
CME technical staff members Andy Gossett, Mark McAnally and James McPhail examined the 3D model of the headband to select the best printers for producing the items. They printed prototypes and provided them to medical staff for assessment.
Once King provided feedback and Ole Miss leadership approved, full production commenced April 2 at the CME.
The CME printers are producing about three batches per day, totaling about 40 prints a day. Gossett agreed to do the changeovers on the printers so others wouldn’t have to get out and potentially be exposed to illness. He also volunteered to come to the center on a 24/7 basis to keep things running.
Others at the university have been contributing to the cause from home. Dave Puleo, dean of the School of Engineering, and Adam Smith, chair of chemical engineering, used their own 3D printers to create more than 25 headbands.
McAnally and McPhail also have been available remotely to assist with technical issues.
Christina Streeter, library manager who works with IDEAlab – a space that includes virtual reality, technology supplies and advanced printing capabilities – has been working to provide 3D prints that also have been included in this effort.
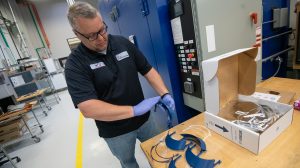
Andy Gossett checks a batch of 3D-printed headbands at the Center for Manufacturing Excellence. Photo by Kevin Bain/Ole Miss Digital Imaging Services
“Since last Thursday (April 2), the process has produced approximately 125 headbands,” Kilpatrick said. “The first delivery provided 70 headbands to the hospital on Monday (April 6), with some of those items being given to one of the local physicians to take along as she travels to New York to assist in giving medical care there.”
Typically, once the prints are completed, CME staff collects the batches, seals them in plastic bags and places them in a closed bin for protection. A staff member contacts King or Peyton Warrington, an assistant hospital administrator, and safely makes the exchange outside the hospital.
Hospital workers are deeply appreciative for the university’s involvement and support at this time, Warrington said.
“They have been so generous toward us in this time of crisis,” she said. “This is certainly a challenging time for people around the world. Individuals are serving in so many inspiring ways.”